introductory
Plastic products are undoubtedly an integral part of modern manufacturing, and injection moulding and extrusion, as two common methods of processing plastics, play an important role in their respective fields. Both technologies have brought countless plastic products into our daily lives, from automotive parts to packaging materials, from medical devices to building components. This article will take an in-depth look at the differences between injection moulding and extrusion, as well as their respective strengths, weaknesses and areas of application, providing readers with a comprehensive understanding of these two key technologies. Whether you are in the manufacturing industry or interested in plastics processing technology, you will gain valuable insights from this article. Join us as we explore this fascinating topic in depth-Injection Vs Extrusion Molding
Table of Contents
Injection vs Extrusion Moulding: Technology Comparison and Advantages and Disadvantage
Injection moulding and extrusion moulding are the two main processing methods used in the manufacture of plastic products, each with their own unique characteristics and areas of application. The following is an in-depth look at the differences between the two technologies, as well as their advantages and disadvantages.
Machine Type
Injection moulding is a process in which a molten plastic material is injected into a mould and formed by cooling and solidifying. The process involves the following key steps:
Heating of the material: Solid plastic pellets are heated to a molten state to form a flowable plastic melt.
Pressure Injection into Mould: The molten plastic melt is injected into a pre-defined mould cavity.
Cooling and curing: The plastic is cooled in the mould and gradually cures into the desired shape.
Advantages of injection moulding
Suitable for complex shapes: Injection moulding is suitable for the manufacture of parts and products with complex shapes, such as those with complex internal structures.
High Precision and Surface Quality: Because injection moulding takes place under high pressure, the products usually have high precision and excellent surface quality, making them suitable for use in areas requiring delicate assembly.
High degree of design freedom: Injection moulding moulds can be customised according to design requirements, providing a high degree of design freedom.
Disadvantages of injection moulding
Higher equipment costs: the establishment of the injection moulding process requires higher equipment and mould costs, suitable for mass production, less suitable for small-scale production.
Extrusion moulding
Extrusion moulding is a process in which a molten plastic material is formed into a desired cross-sectional shape by squeezing it through a die. The following are the key steps in extrusion moulding:
Raw material heating: Solid plastic pellets are heated to a molten state.
Extrusion Machinery: The molten plastic melt is passed through the extrusion machinery and extruded through the die to form the desired cross-section.
Cooling and curing: The plastic is cooled in the mould and cured into a long strip.
Advantages of extrusion moulding
Continuous Production: Extrusion moulding is suitable for continuous production and is suitable for the manufacture of long products such as plastic pipes and rods.
Suitable for composites: Extrusion moulding can be used to produce plastic composites with stable moulding properties, suitable for high performance requirements.
Disadvantages of extrusion moulding
Consistency Challenges: Due to the long production cycle of extrusion moulding, temperature and pressure variations during the production process may affect the consistency of the product.
By comparing the advantages and disadvantages of injection moulding and extrusion moulding, it is possible to select the appropriate processing method for the specific product requirements and production scale to achieve the best manufacturing results. Whether it is the manufacture of complex parts or the need for continuous production, injection moulding and extrusion moulding play an irreplaceable role in modern manufacturing.
Areas of application for injection moulding and extrusion moulding
Plastics processing technologies play a key role in a wide range of industries, and injection moulding and extrusion, the two main methods, show unique advantages in different areas. Below are examples of how these two technologies are used in specific areas.
Areas of application for injection moulding
Automotive Manufacturing: Injection moulding plays an important role in the automotive manufacturing industry. It is used to manufacture a variety of automotive parts such as instrument panels, door panels, and interior parts. Its high precision and surface quality make it ideal for producing complex parts.
Medical Device Manufacturing: In the medical field, injection moulding is used to manufacture fine medical device parts such as syringes, infusion sets, surgical instruments, etc. Their precision and sterility are critical for medical devices.
Areas of application for extrusion moulding
Construction: Extrusion moulding is widely used in the construction industry. It is used to manufacture plastic pipes, window frames, door frames and other long components. Extrusion moulding technology meets the need for building materials that are durable and malleable at the same time.
Packaging: Extrusion plays an important role in the packaging sector. It is used to manufacture a wide range of packaging materials such as plastic film, cling film, plastic bags and more. Extrusion moulding is capable of producing a range of different shapes and sizes of packaging products.
By choosing the right moulding technology, manufacturers in different sectors can meet their product needs and increase productivity. Whether it’s automotive, medical devices, construction materials or packaging products, injection moulding and extrusion contribute significantly to innovation and development in a variety of fields.
Conclusion: Options and developments in injection moulding and extrusion moulding
A comparison of the two plastics processing technologies, injection moulding and extrusion, makes it clear what their strengths and weaknesses are in different aspects as well as their respective areas of application. In choosing the right moulding technology, a number of factors such as product requirements, production scale and performance need to be fully considered.
Injection moulding is making its mark in areas such as automotive manufacturing and medical devices with its ability to accommodate complex shapes, high precision and excellent surface quality. However, the high cost of equipment may limit its use in small-lot production.
Extrusion moulding, on the other hand, plays an important role in the construction and packaging sectors, characterised by its ability to produce continuously, its suitability for long strips and its consistency in manufacturing composites. However, long production cycles can pose some challenges to consistency.
Choosing the right moulding technology is an important part of ensuring product success. As manufacturing technology continues to evolve, injection moulding and extrusion will continue to evolve to provide even more superior solutions for different types of products and industries. In the pursuit of innovation and quality, a deeper understanding and flexibility in the use of these technologies will provide manufacturers with more opportunities and competitive advantages.
Related News
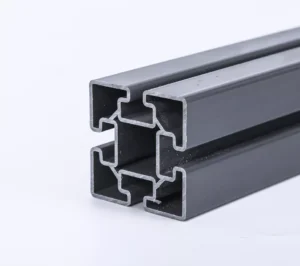
What Is Plastics Extrusion?
Plastic extrusion is a continuous mass production process, also often referred to as plasticised extrusion. This process is currently used in a wide range of industries. The most common example
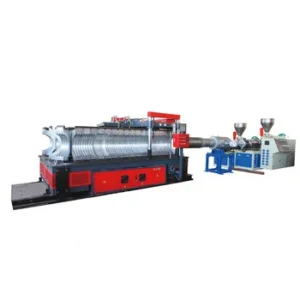
The Benefits of Using Corrugated Pipe Machines in Construction Projects
Introduction Corrugated pipe machines play a vital role in modern construction projects and their widespread use has become the norm in the industry. In the construction sector, corrugated pipe machines
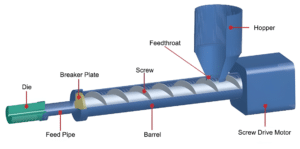
What is plastic extrusion and how does it work?
Plastic is one of the best things man has ever invented and made to use. It is cheap to manufacture, lightweight, and strong. For these reasons, plastic has a wide