introductory
Types of Plastic Extrusion Processes & Material Selection-Plastic extrusion processes include a wide variety of technologies for manufacturing plastic products with different sizes, shapes, and properties. Selection of the appropriate extrusion method and plastic material is critical to achieving the desired functionality, appearance and performance characteristics of the end product.
There are several different types of plastic extrusion processes, each customized for specific applications and material requirements. By carefully selecting the appropriate process and materials, manufacturers can produce a wide range of products, including pipe, profile, sheet, and film, to meet the needs of a variety of industries, from construction to automotive to packaging.
Table of Contents
Types of Plastic Extrusion Processes
Although plastic extrusion machines vary in the way they extrude plastic, the basic concept is the same. The type of plastic extrusion process depends on the complexity of the mold shape. Some types are better at handling complex patterns than others.
Here are the four main process types used by manufacturers in the market today.
Pipe Extrusion
The process of extruding plastic for pipe extensions is the same until the die portion is extruded. This method is suitable for tubing and other hollow items such as long pipes and water pipes. It is also suitable for making drinking straws and medical tubing.
The operator places a mandrel or pin into a mold and then applies positive pressure through the pin into the interior space to make the hollow section. When there are multiple holes, the manufacturer places multiple pins in the center of the mold. How many pins you need depends on how many holes you want.
Also, in this case, the air pressure for the pins generally comes from a different source, making it easy to change the size of each hole.
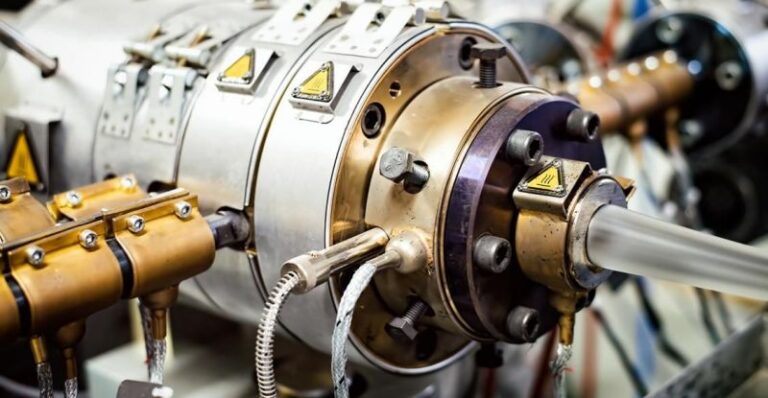
People often use blown film extrusion to make items such as shopping bags. Just like the pipe plastic extrusion method, the die is the main difference between blown film extrusion and regular extrusion.
A blown film extrusion die is a tall cylinder with a round hole in it. These holes are as small as a few centimeters and as large as over three meters. In this process, a set of pressure rollers pulls the molten plastic out of the die.
In most cases, the pressure rollers are four to twenty meters above the mold. The exact height of the rollers depends on the degree of cooling required. In addition, the wall thickness or thickness of the film depends on how fast the rollers are moving. As the film moves upward, an air ring around the die head helps cool the film.
A hole in the center of the die head pumps compressed air into the center of the extruded round plastic. This creates air bubbles. This causes the circular cross-section of the extruded plastic to grow by a certain amount. This number, also known as the “blow-up ratio,” can be a few percent to more than 200 times the original width.
Finally, a nip roller helps flatten the bubbles to make a double-sided film that is half the width of the bubble diameter. This double-sided film can be cut into different shapes, wound onto rolls, or printed. By sealing it with heat, it can also be used to make bags and other things.
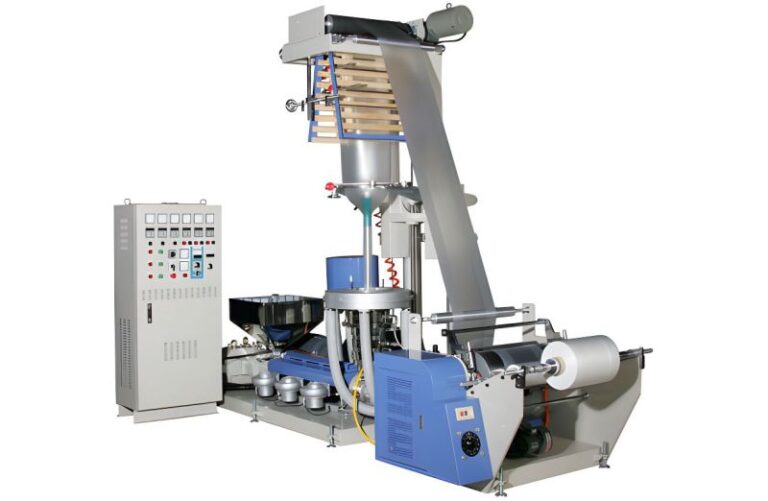
Sheet film extrusion
This process is very similar to blown film extrusion, but the way of making the desired shape is different. In this type of extrusion, the primary method of obtaining the desired shape is to pull and roll the material. This involves determining the roughness or smoothness of the surface of the sheet as well as the thickness.
The rolling process ensures that the product has the correct shape and helps in cooling and permanent solidification.
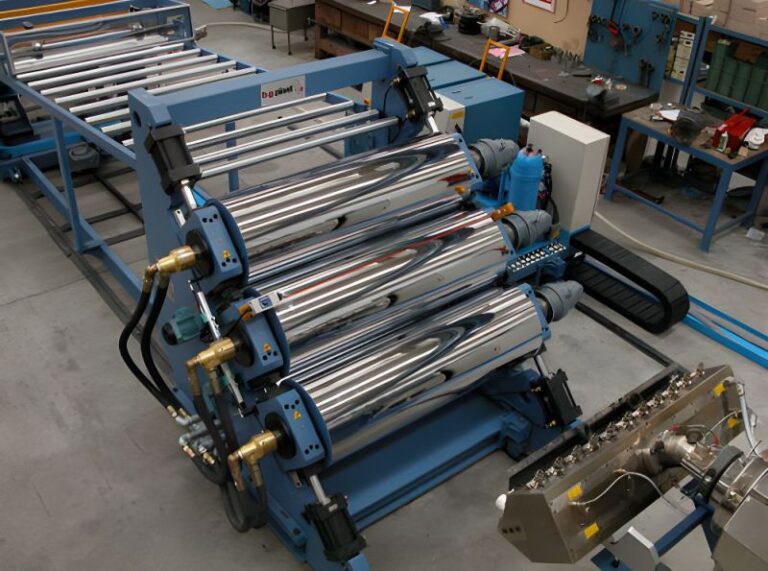
Over-jacketing Extrusion
This plastic extrusion process is suitable for manufacturing insulated wires. The purpose of this process is to apply a plastic jacket to the material. Pressure and sheathing are the two main plastic extrusion tools used to coat wires.
Both tools have their uses, but which tool is used to coat the wire with plastic depends on how tightly the plastic needs to be to the wire.
If there needs to be close contact or adhesion between the wire and the material, a pressure tool is the best method. However, if tight contact is not required, sheathing is preferred.
The most important difference between these tools is the position of the pins on the mold. When the pins are inserted all the way to the edge of the mold, it is called “jacketed tooling.” With pressure molding, on the other hand, the end of the pin stays inside the crosshead. This means that the wire is covered by melted plastic while it is inside the mold. In this case, the pressure increases as the wire and liquid plastic come out of the mold.
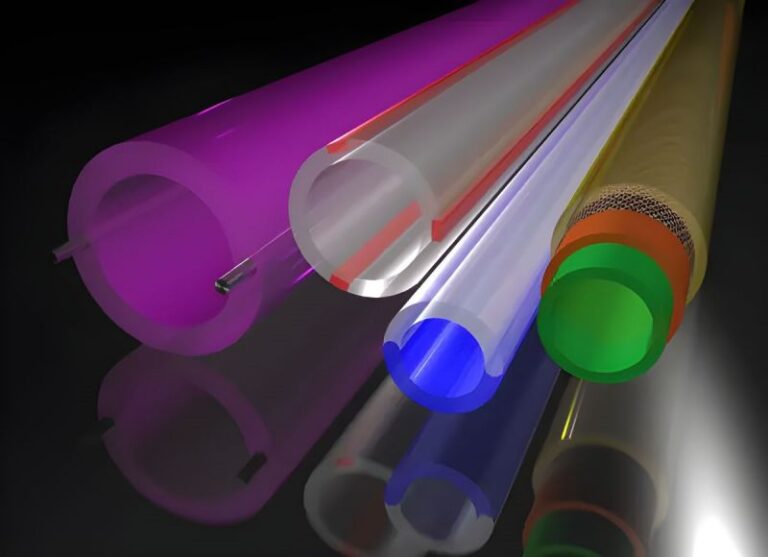
Material Selection for Plastic Extrusion
Plastic extrusion can be done using a variety of materials. Choose which material to use based on the product you need. The following is a list of various materials that can be used for plastic extrusion.
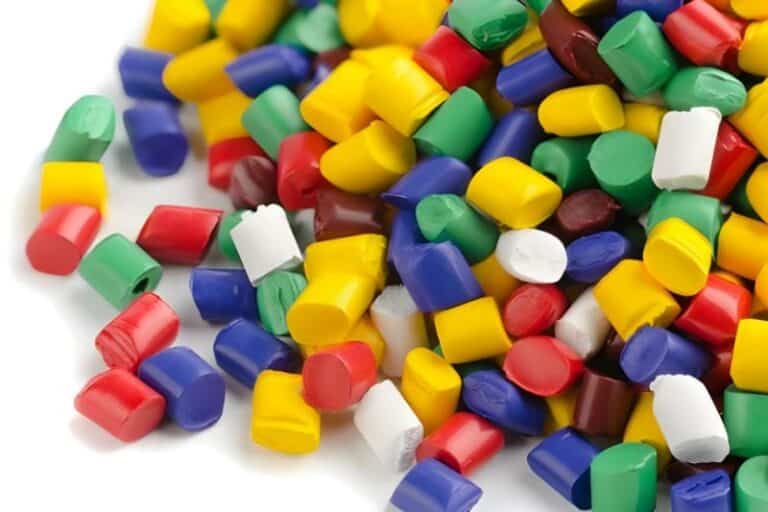
- ABS (Acrylonitrile Butadiene Styrene): Styrene is polymerized to make ABS, and the combination of acrylonitrile and polybutadiene makes it stronger than the polystyrene itself. the styrene in ABS makes the surface waterproof and glossy, while the polybutadiene makes it shiny no matter what the material is. The polybutadiene, on the other hand, makes it tough no matter what the weather.
- Acrylic: this compound has a wide range of uses in industry and can be used in place of glass due to its light transmittance. Acrylic strikes the perfect balance between weatherproofing, sturdiness, and transparency. It can also be colored, diffused, or frosted to suit your needs. It’s like acrylonitrile-styrene-acrylate-ASA.
- PVC (Polyvinyl Chloride): This is one of the most used plastic materials in the world. It can be used in many ways in almost all industries. There are two main types of polyvinyl chloride: soft PVC and rigid PVC.
- Soft PVC: This material is cheap and versatile and is very common. It is also the perfect combination of weather resistance, tear resistance, and tensile strength.
- Rigid PVC: Rigid PVC is impact resistant and remains stable in sunlight. This material is used to make pipes and special plastic profiles such as refrigerators, doors, and windows. Because of its hardness, it can be used to replace wood and metal in many cases.
- CPVC (Chlorinated Polyvinyl Chloride): CPVC has a natural color and UL94 flame retardant properties. It also has good stiffness, high-temperature properties, and impact resistance.
- Mineral-Filled Polypropylene: This material works well regardless of temperature. It remains constant at many different temperatures.
- Polycarbonate: This material combines hardness, abrasion resistance, impact resistance, coloring ability, and high and low-temperature performance.
- Styrene: Like polycarbonate, styrene is a material that combines toughness, strength, stiffness, and coloring ability.
- TPA (thermoplastic alloy): This synthetic material is well suited for weather stripping, gaskets, and other items. It has good compression permanent deformation, is stable at low temperatures, and can be stretched.
- Polyethylene: This is a great material because it is strong, can be colored, and works well at low temperatures.
- TPV (Thermoplastic Vulcanized Rubber): This material does not tear easily, can withstand the elements, and is flexible at low temperatures. It also has good tensile strength.
- Polypropylene: This material is strong, does not tear easily, can be colored, and works well at low temperatures.
Related News
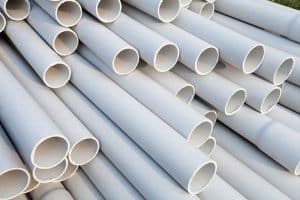
Difference Between CPVC And PVC
As the performance requirements of piping systems for construction and industrial projects continue to increase, choosing the right piping material has become particularly important. cpvc and pvc piping have become
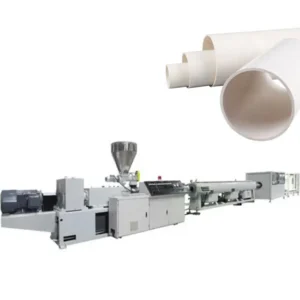
High-Performance Plastics Extruders Lead To Breakthroughs In New Material Applications
introductory High-performance plastics extruders lead the way to breakthroughs in new material applications – In modern manufacturing, high-performance plastics extruders are leading the way to revolutionary breakthroughs in new material
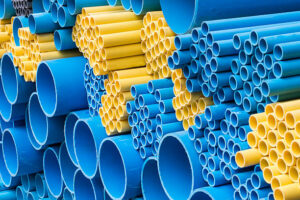
PVC Vs Corrugated Drain Pipe
Drainage systems are a critical part of residential and industrial projects. The right choice of pipe not only affects the overall efficiency of the project, but also determines the system’s