introductory
The basic principles of pipes extrusion– Plastic pipe extrusion process is an important manufacturing method used to produce plastic pipes for various applications. The basic principles involve heating, melting and extruding solid plastic pellets to form the desired pipe shape. Let’s take a closer look below.
Table of Contents
Plastic Pipe Extrusion Process Introduction
Plastic pipe extrusion process is an important plastics processing method by which a wide range of plastic pipes can be produced for different applications. The process involves heating, melting and extruding plastic granules to eventually form the desired pipe shape. Due to its high degree of customisability and versatility, the plastic pipe extrusion process plays an important role in construction, industry and other sectors. Its high degree of customisability and adaptability enables the production of plastic pipes to meet a wide range of needs, providing efficient, reliable and cost-effective solutions for a variety of industries.
- In the construction sector, plastic pipe extrusion is widely used in the manufacture of various piping systems, such as water supply pipes, drainage pipes and cable protection pipes. Plastic pipes are lightweight, corrosion- and chemical-resistant and easy to install, making them an ideal alternative to traditional metal pipes. In addition, plastic pipes can also meet the requirements of construction projects for hygiene, environmental protection and durability.
- In the industrial sector, the plastic pipe extrusion process is used to produce industrial pipes, chemical pipes, gas supply pipes, etc. These pipes need to meet more stringent requirements. These pipes need to fulfil more stringent requirements such as resistance to high pressure, corrosion and temperature. Plastic pipes play a key role in industrial production as these properties can be realised with different materials and process parameters.
- In addition to construction and industry, plastic pipe extrusion processes are used in a wide range of other fields. For example, in agriculture, plastic pipes for irrigation systems and farm drainage systems help to increase the efficiency of agricultural production. In urban infrastructure, plastic pipes for sewage treatment, storm water drainage and communication cable protection are also indispensable.
Composition of plastic pipe extrusion line
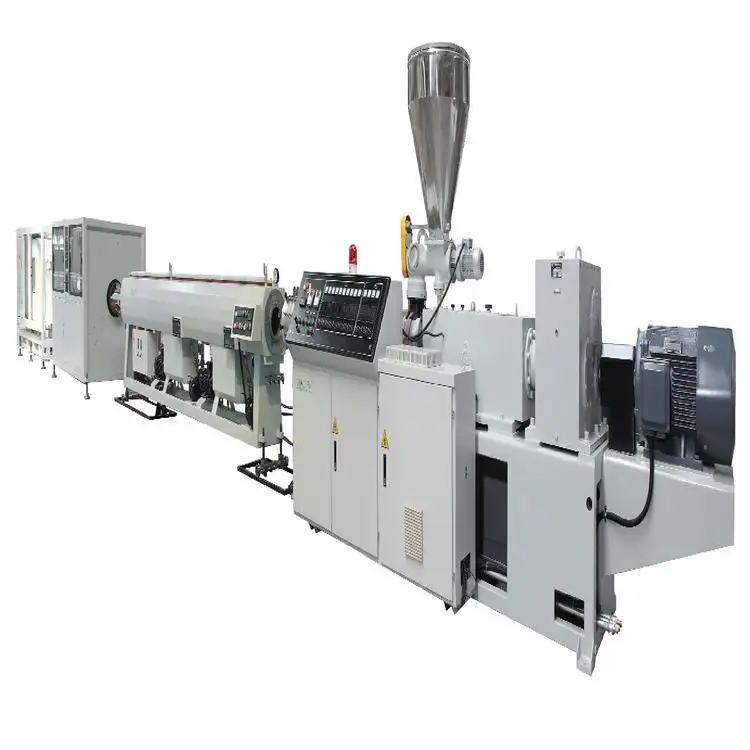
A plastic pipe extrusion line is a complex process system consisting of several key components, each of which plays an important role in the production process. The following are the main components of a plastic pipe extrusion line:
Extruder
The extruder is the core equipment of the entire line and is responsible for heating and melting the plastic raw material and extruding it through the die head into the desired shape of pipe. The extruder usually consists of a screw, a heating zone, a cooling zone, a motor and a control system. The screw is responsible for heating and pushing the plastic pellets to melt and form a uniform molten material.
Die Head
The die head is the component that moulds the molten plastic material into a specific cross-sectional shape. Its design and construction determine the shape and size of the final pipe. The die head usually consists of multiple extrusion holes through which the molten plastic is extruded to form the initial shape of the pipe.
Cooling System
A cooling system is used to rapidly cool and cure the extruded molten plastic to maintain its desired shape and size. Cooling systems can include components such as water showers, cold air blowers and cooling rollers to ensure that the pipe cools quickly and remains stable after extrusion.
Haul-off Equipment
Haul-off equipment is used to pull the extruded plastic pipe from the die head and to control the pipe’s haul-off speed to ensure consistent size and appearance. Haul-off equipment typically uses belts, straps or tyres to provide consistent traction.
Cutting Equipment
Cutting equipment is used to cut the extruded pipe to the desired length. Cutting can be done with knives, saws, etc., to ensure that each pipe is the exact length it needs to be.
Winding Equipment
For the production of long pipes, the winding equipment is used to wind the extruded pipes into coils for easy transport and storage.
Control System
The entire production line requires a precise control system to monitor and adjust the operation of the extruder, die, cooling system, haul-off equipment and other components. Modern control systems often include automation and data acquisition to optimise the process and ensure product quality.
The components of a plastic pipe extrusion line from PLASTIC EXTRUSION MACHINES work closely together to ensure that the plastic raw material is processed into a pipe product that meets specifications. The performance and operation of each component has a significant impact on the quality and efficiency of the final product. Understanding the function and role of these components is critical to understanding how a plastic pipe extrusion line works.
Basic Principles of Plastic Pipe Extrusion
Plastic pipe extrusion is a process commonly used to manufacture plastic pipe that involves a series of precise steps and processes to ensure the quality and performance of the final product. The following are the basic process principles of plastic pipe extrusion, covering key aspects such as plastic material selection, pretreatment, extrusion process, cooling and shaping, and haul-off and cutting:
1. Plastic material selection: In plastic pipe extrusion, the first step is to select the appropriate plastic material for the desired application. Different plastic materials have different performance characteristics, such as corrosion resistance, high temperature resistance, compressive strength. When selecting the material, it is necessary to consider the environment and the purpose for which the pipe will be used to ensure that the final product will meet the requirements.
2. Pretreatment: Plastic pellets are usually pretreated prior to extrusion. This involves drying the raw material to remove moisture from it, which can cause bubbles and defects during extrusion. In addition, different types of plastic pellets may need to be blended, if required, to obtain the desired physical and chemical properties.
3. Extrusion process: In an extruder, the pre-treated plastic pellets are heated, melted and then extruded through a die. During the heating and melting process, the plastic pellets are turned into a molten state that allows them to be shaped through the die head to form the initial pipe profile. The extruder usually consists of a heating zone, a melting zone and a cooling zone to ensure gradual heating and melting of the material.
4. Cooling and Shaping: Once the molten plastic is extruded through the die head, it enters the cooling system. During the cooling process, the plastic is rapidly cooled to maintain its desired shape and size. Cooling also helps to solidify the plastic and ensures that the final product has the required strength and stability.
5. Drawing and cutting: After cooling, the extruded pipe enters the drawing equipment. The haul-off equipment stretches the pipe to the desired length and helps to further shape it. Once the pipe reaches the desired size, it is cut to the appropriate length and collected, ready for the subsequent processing stages.
By following these basic process principles, a plastic pipe extrusion line is able to produce a high quality pipe product that meets specifications. Precise control of each step and proper parameter settings are critical to ensuring the quality, appearance and performance of the pipe.
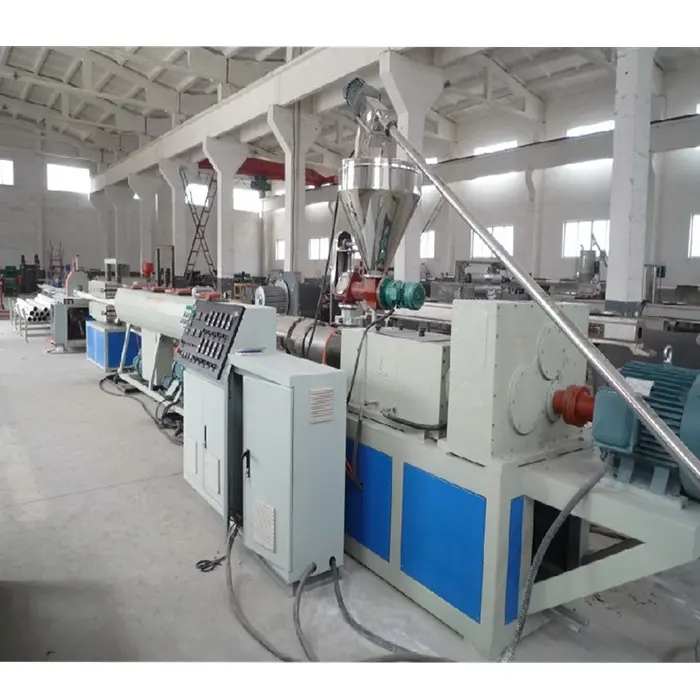
Key Strategies to Improve Productivity
Plastic pipe extrusion lines can achieve higher productivity and quality standards by adopting the following key strategies. This not only reduces scrap rates and maintenance costs, but also increases capacity and customer satisfaction, allowing companies to remain competitive in a highly competitive market.
Optimization of process parameters: In plastic pipe extrusion line, optimization of process parameters is the key to improve efficiency. By accurately adjusting parameters such as extrusion temperature, extrusion speed, extrusion pressure, etc., a more stable extrusion process can be realized, reducing scrap rates and increasing production and product quality.
Quality control: Emphasize the importance of quality inspection and testing to ensure that the extruded plastic pipes comply with standards and specifications. The introduction of automated testing equipment, such as dimensional gauges and visual inspection systems, allows for real-time monitoring of product quality, early detection of problems and action to be taken to minimize rejects and improve production efficiency.
Raw material management: Ensuring the quality and consistent supply of raw materials is critical to the success of extrusion production. Establish stable supply chain relationships and communicate regularly with suppliers to ensure that raw materials meet specified standards. The use of advanced raw material testing methods, such as infrared spectroscopy and melt index testing, ensures consistency from batch to batch and avoids quality fluctuations.
Maintenance: Regular maintenance and upkeep of your plastic extrusion equipment can reduce downtime, extend equipment life and keep your line running efficiently. Develop a detailed maintenance program that includes cleaning the equipment, lubricating parts, and replacing worn parts to ensure that the equipment is in optimal condition. Addressing potential breakdowns and problems in a timely manner reduces line downtime and increases productivity.
Industry trends and future outlook
Plastic pipe extrusion technology, a key part of the plastics processing sector, is undergoing a continuous evolution to adapt to changing market demands and global sustainability trends. The future will also continue to usher in innovations in sustainability, smart manufacturing, customized production, digital transformation and new material applications. These trends will lead the plastic pipe extrusion industry to a greener, more efficient and diverse future as society and market demands continue to evolve. Manufacturers and technology developers are expected to contribute to the industry’s sustainable growth and progress by actively exploring these areas.
Conclusion
The basic principles of the plastic pipe extrusion process are key to achieving efficient production and quality products. By understanding these principles in depth and applying them correctly, the Plastic Pipe Extrusion Line’s productivity and product quality can be significantly improved. will be the key to achieving efficient production, superior quality and market competitiveness.
Related News
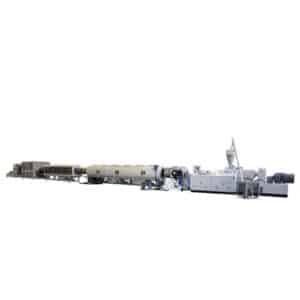
How Does A Plastic Extrusion Machine Work?
As a manufacturer of PVC/PP/PE and other composite pipes, it is likely that you have already learned about extruders and operated one. Whether you already have a machine or are
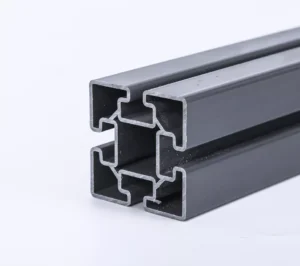
What Is Plastics Extrusion?
Plastic extrusion is a continuous mass production process, also often referred to as plasticised extrusion. This process is currently used in a wide range of industries. The most common example
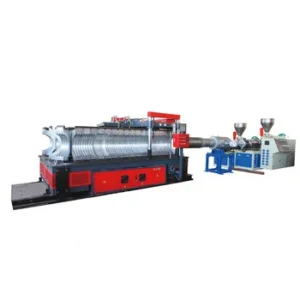
The Benefits of Using Corrugated Pipe Machines in Construction Projects
Introduction Corrugated pipe machines play a vital role in modern construction projects and their widespread use has become the norm in the industry. In the construction sector, corrugated pipe machines